Un proyecto de I+D liderado por la compañía ourensana Extraco para el aprovechamiento de residuos de plantas asfálticas ha logrado el reconocimiento de la Fundación Renault Group España y del Club de Excelencia en Sostenibilidad como
Extraco, mejor práctica en Movilidad Sostenible y Accesible
En qué consiste Alfiller
La idea, denominada Alfiller, consiste básicamente en la reutilización del filler de recuperación resultante del proceso de fabricación del asfalto en el desarrollo de productos de base cemento para distintos usos.
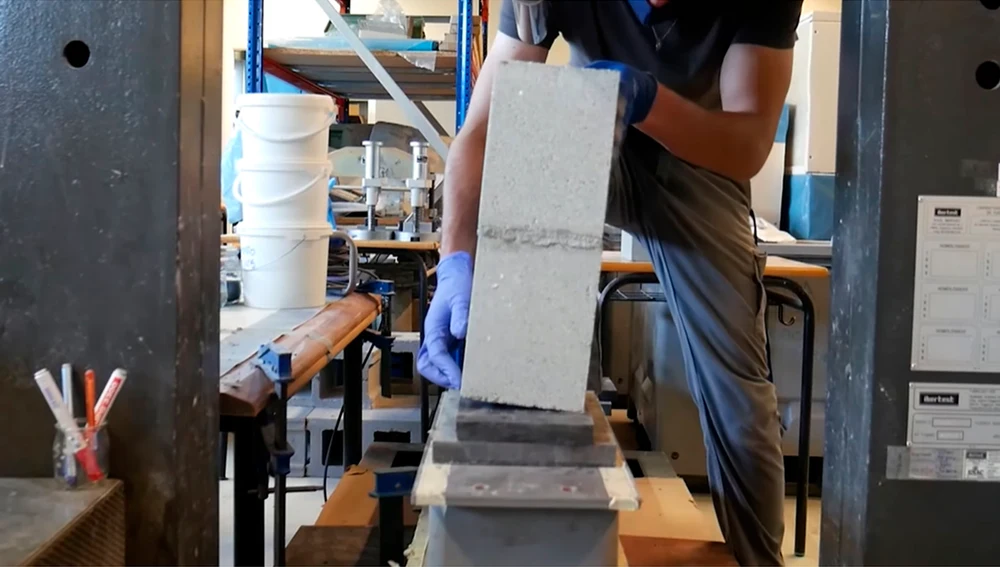
En España existen 190 plantas asfálticas en caliente, con una producción que supera los 15 millones de toneladas y un 4% de filler de recuperación, lo que implica alrededor de 600.000 toneladas anuales de residuo que deben gestionarse adecuadamente para su depósito en vertederos, con el consiguiente impacto económico y ambiental, estimado en más de 5 millones de euros.
Un consorcio empresarial encabezado por Extraco y en el que participaron también las firmas Prefhorvisa, Galaicontrol y Renga, contando con el apoyo del grupo de Construcción-gCONS de la Universidad de La Coruña, desarrolló un completo proceso de análisis físico, químico y mecánico de ese filler de rechazo y constató su adaptación para la elaboración de nuevos morteros de albañilería, revestimiento y hormigones de relleno para bloques prefabricados, usos con una notable salida comercial en el sector de la construcción.
La fabricación de mezclas bituminosas en caliente es un proceso continuo donde los áridos son sometidos a una operación de secado y calentamiento.
Después pasan por un cribado destinado a separar el material en fracciones de diferente tamaño y depositarlo en tolvas calientes para su almacenamiento, antes de pasar a la cámara mezcladora y de la incorporación al proceso del betún, último paso antes de obtener la mezcla asfáltica. El problemático residuo, el filler de recuperación, procede del cribado y mezclado de los áridos.
El proyecto desarrolló inicialmente un completo procedimiento de análisis y estudio para lograr la caracterización física, química y mecánica del filler, pensando en sus posibles aplicaciones. Y una vez determinados esos resultados se definieron, por un lado, dos tipos de mortero con cemento, uno de albañilería y otro de revestimiento, ambos para su aplicación en edificación, y por otro se diseñaron hormigones autocompactantes para aplicaciones in situ y de consistencia más seca para elementos prefabricados. Para este último objetivo se tuvo muy en cuenta el abanico de posibilidades abierto para las empresas de prefabricados de hormigos desde la crisis iniciada en 2008.
Además de distintos ensayos específicos para testar los resultados, se proyectaron muros prototipo para la aplicación directa de los materiales estudiados. De esta forma se pudo calibrar la calidad del producto resultante en el relleno de bloques con hormigones muy fluidos, empleándose asimismo los morteros de revestimiento y albañilería para la ejecución de las propias paredes. El resultado final arrojó datos lo suficientemente satisfactorios tanto medioambientalmente como para la propia competitividad de las empresas integrantes del consorcio.
El proyecto se desarrolló entre los años 2018 y 2021, y a su término llamó la atención de la Fundación Renault Group España y del Club de Excelencia en Sostenibilidad. En un evento celebrado en la sede de Renault Group, en Madrid, la constructora ourensana fue distinguida en la categoría de Pymes/Emprendedores de la novena edición de los Premios a la Mejor Práctica en Movilidad Sostenible y Accesible. Además de Extraco fueron reconocidas Sagulpa (Sociedad Municipal de Aparcamientos de Las Palmas de Gran Canaria) e Iberdrola.